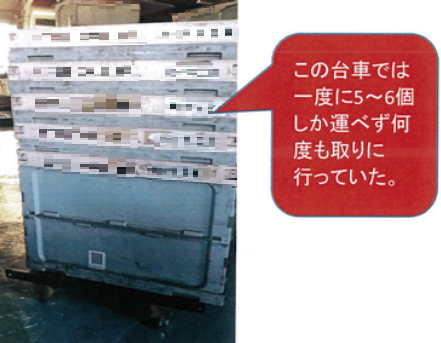
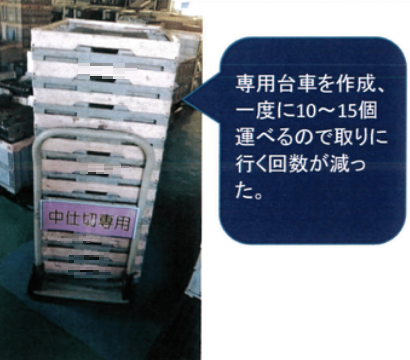
【結果/効果】
(なにが)
専用台車を作成したので
(どうなった)
1日に5~6回取りに行っていたのが
1日2~3回に短縮された。
【専門家コメント】
改善活動お疲れ様です。
今回の改善では、運搬頻度が高い「中仕切り」を運ぶ専用台車を導入した事例であり、運搬作業の効率化が図られた点が大きなポイントです。
台車を専用化したことで、一度に運べる量が2〜3倍に増加し、運搬回数の削減という明確な成果が得られました。運搬作業は生産に直接関与しない付随作業のため、その回数や時間を減らすことが、作業の効率化と収益性の向上に直結します。
■改善のポイント
専用台車の導入により、1回あたりの運搬量が増え、運搬回数が減少しました。
台車に「中仕切り専用」と明示しているため、別の用途で使われるのを防止でき、作業の混乱を回避することができています。
■更なる改善案
さらなる改善を目指すのであれば、「中仕切り専用台車」を定位置管理することをお勧めします。保管場所を明確化し、台車の置き場を指定することで、探す時間(ムダ)を削減することが可能です。これにより、作業の流れがさらにスムーズになり、台車の使用効率が向上します。定位置管理は、5S活動(整理・整頓)にもつながるため、工場全体の改善にも効果的です。