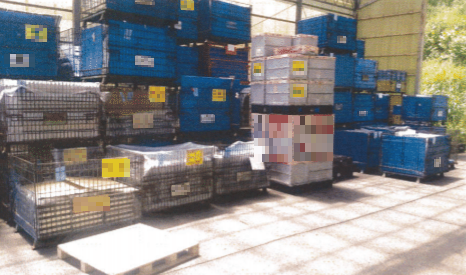
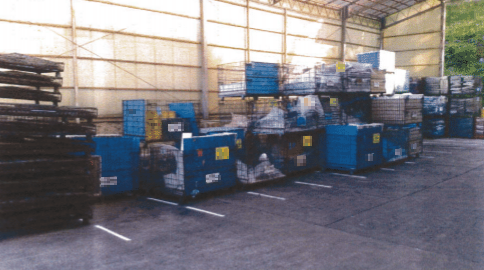
【結果/効果】
(なにが)
おおよその置場で統一されていなかった。
(どうなった)
ラインを引き、機種ごとに統一させた。
【専門家コメント】
改善活動お疲れ様でした。
いままでは、「空いている所にとりあえず置いておこう」というルールから
「きっちりと機種ごとに置き場を決めた」ルールへの改善ですね。
とてもすばらしい改善だと感じました。
さらなる改善に向けての提案ですが、その場に行ってから何がどこにあるかを確認するのではなく
遠くからでも何がどこに置かれているのか分かるように「大きな看板」を背面の壁に貼り付けたり、
天井から吊るしたりすると、もっとわかりやすくなると思います。
分け分けは、5S活動のなかで非常に重要なポイントです。
引きつづき、横展開も含めて「わけわけ」がんばってください!!