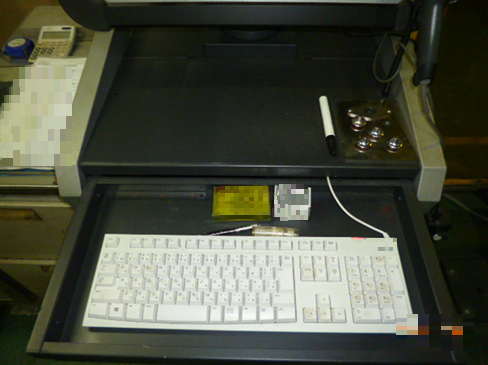
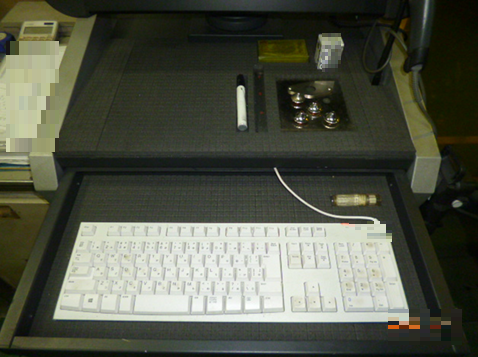
【結果/効果】
(なにが)
形跡整頓をおこなったので物の取出しが
(どうなった)
改善前 10秒 、改善後 5秒、
5秒短縮×月、100秒
1カ月あたり:100秒削減
〈月100円削減〉
【専門家コメント】
これまで操作盤の上に乱雑に置いていた工具備品類を
ぷら板を使用して形跡整頓を実現した事例ですね。
形跡整頓したことによって
収まる場所に収まるものが収まるという
整頓の基本ができました。
これがまさに、モノの置き方の標準化です。
とても素晴らしい改善をありがとうございます。
さて、さらなる改善に向けてのアドバイスですが、
他の物を置かれないように、何の置き場かを
明示してみてはどうでしょう。
複雑な形の工具なら間違えようがないのですが、
単なる四角い形だと、そこにはまるものはなんでも
置くことができてしまいます。
容易な形だからこそ、しっかりと明示していただければと思います。
がんばってくださいね!!
次回の報告を楽しみにしていますね。