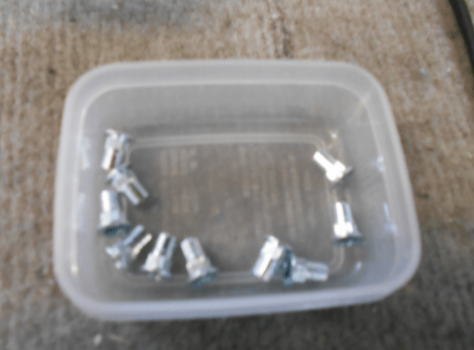
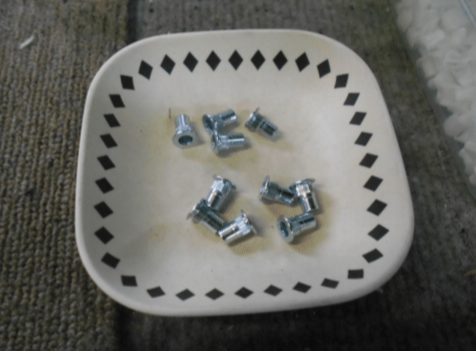
【結果/効果】
(なにが)
容器を間口の広い小皿に変更。
(どうなった)
ナットが掴み易くなり、ナットを取る時間が
短縮された。
無くなったことで、1日約12秒の短縮に繋が
った。
【専門家コメント】
以前は深さのある長方形の容器を使用していたところ、
間口の広い浅い小皿に変更した改善ですね。
小皿には軽い傾斜がついており、ナットが自然に容器の中心に集まる工夫が施されているため、ナットを掴みやすくなり、取り出し時間が短縮されたとのこと。
これにより、1日あたり約12秒の時間短縮を実現したとのことで、
小さな改善でも作業効率の向上につながる素晴らしい取り組みです。
細かい部分に目を向けて改善を進めていただき、ありがとうございます!
次に考えていただきたいのは、この改善がさらに効果的に運用され、
ほかの作業にも波及できる仕組みです。以下の点を意識してみてください:
- 他の作業工程にも応用できないか検討
今回のように「取り出しやすさ」を追求した改善は、他の部品や工具の
扱いでも応用できるかもしれません。例えば、他のパーツや小物にも
同様の浅い容器や傾斜のついたトレイを使用することで、さらなる
作業効率の向上が期待できます。現場をよく観察し、他にも改善できる
点がないか探してみましょう。 - 作業台全体のレイアウト最適化
ナットの取り出し作業が改善されたことで、作業全体の流れもさらに
効率化できるかもしれません。作業台の配置や他の工具・部品の配置を
見直して、最短距離で作業が進められるレイアウトを検討してみてください。
細かい時間短縮が積み重なると、大きな効果につながります。 - 改善のフィードバックと継続的な見直し
今回の改善効果が実際に現場でどう評価されているか、作業者からの
フィードバックを定期的に収集することで、新たな問題点やさらなる
改善点が見つかることがあります。また、時間短縮効果が維持されているか、
定期的にモニタリングし、必要があればさらなる調整を行いましょう。 - 他の容器やツールの選定基準の見直し
今回の小皿の変更は非常に効果的ですが、他の容器や工具についても
使いやすさや作業効率を向上させるための基準を見直してみると良いでしょう。
たとえば、軽量化やコンパクト化、持ちやすい形状など、現場に合わせた
ツールの選定基準を明確にし、さらなる改善につなげることができます。
今回の改善は、日常的な作業の中で小さな時間短縮を実現した大きな成果です。
このような工夫を積み重ねていくことで、職場全体の作業効率がさらに向上するはずです。
引き続き、他の部分にも目を向けて、さらなる改善に挑戦してください。
次の報告書を楽しみにしています!