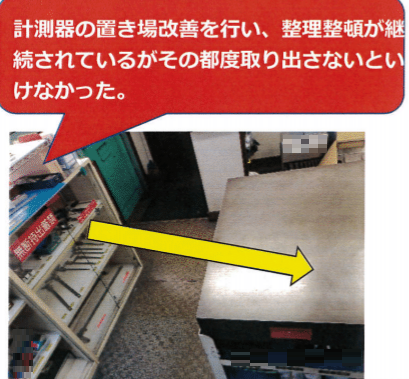
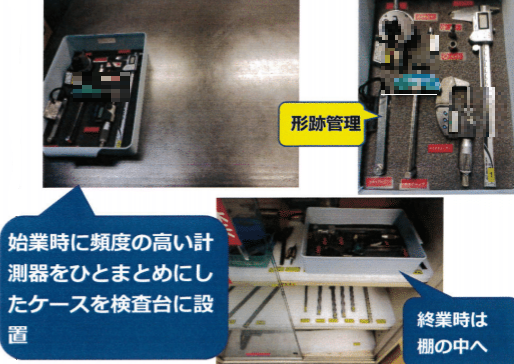
【結果/効果】
(なにが)
計測器をその都度棚から取り出さないといけない
(どうなった)
使用頻度の高い計測器を形跡管理しケースごと検査台に
移動した。移動距離が短縮された。
【専門家コメント】
検査する際に必要な工具を都度ひとつずつ取り出していたものを
使用頻度の高いものを一つのケースにまとめて
取り出すようにした改善ですね。
しかも、形跡整頓で個別管理までされている点は
本当に素晴らしいと感じました。
素晴らしいアイデアをありがとうございました。
これによって、作業効率は大幅にアップしたこと間違いなしですね。
この改善は、工具における「必要なものを必要な時に必要な量だけ用意する」
ジャストインタイムの考え方を体現した内容になっていると感じました。
部品や製品だけでなく、工具類にこの考え方を導入されることは
とても素晴らしい取り組みです。
ぜひ、この考え方をほかの改善活動に活かしていただければと思います。
さらなる改善がどんどん進んでいくこと間違いなしです。
では、次回の改善報告も楽しみにしています!