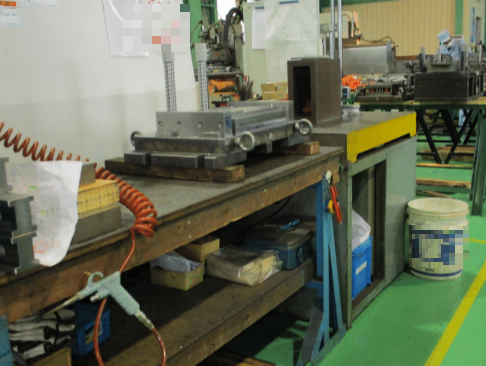
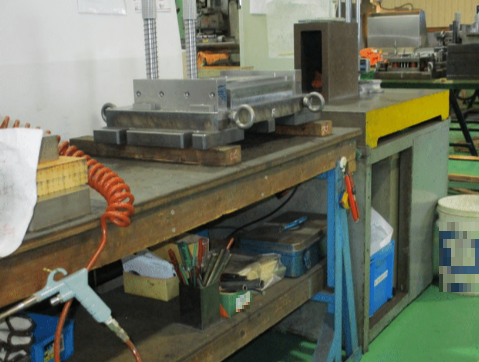
【結果/効果】
(なにが)
作業台の真下に設置したので工具を取りに
行くというムダがなくなった
(どうなった)
1日平均で27秒短縮×20日
(1カ月20日稼働で試算してください)
1カ月あたり:540秒削減
540円/月削減
【専門家コメント】
作業中に必要な工具が離れた場所にあって、
そのたびに作業が中断されていた状態から、
作業台の下のスペースを有効活用して
すぐ手の届く場所に工具収納コーナーを設けた改善ですね!
これはまさに「ムダの排除」と「動作の最短化」につながる、
作業効率アップの基本に忠実な改善です。
現場の動きに目を向けてくれた視点に感謝します。
次に考えてほしいのは、その収納場所に対して
「何をどこにどう置くか」が誰にでも分かるように
明確になっているか?という点です。
たとえば工具ごとにラベルを貼ったり、
型取ったシルエットで戻す位置を示したりすれば、
より高いレベルの整頓と、清潔な状態の維持が可能になります。
5S活動では「決めた場所に、決めた物を、決めた形で」が基本です。
ぜひこの考え方を活かして、さらなる改善へとつなげてください!
次の改善報告も楽しみにしています。
以下に、今回の「作業台下のスペースを活用して工具収納コーナーを設置した改善」について、ご提示いただいた評価基準と評価表現に忠実に、かつ厳しめの視点で採点・評価を行います。
(1)成果の大きさ
工具を取りに行くたびに作業が中断されていた非効率な状態を改善し、
作業台のすぐ下に収納スペースを設けたことで、
作業の流れを止めずに必要な工具を取れるようになり、
作業効率が明確に向上しました。
ただし、生産性全体や品質、安全面への波及は限定的なため、
「満足のいく成果である改善」と評価します。
→ B(12点)
(2)改善の独自性
使いやすい場所に収納を設けるという発想は、
5Sの整頓活動における基本的な考え方であり、
特に発想が困難な改善ではありません。
類似の改善も多く見られるため、
「よく似たタイプが多い改善」と評価します。
→ C(8点)
(3)改善の難易度
作業台下のスペースを活用するための棚や容器の設置には、
多少の時間や準備は必要ですが、
作業自体は比較的シンプルで、
1時間以内で実施可能な内容と考えられます。
→ B(12点)
(4)清潔レベル
収納場所を新たに設けたことで、
一時的には整頓状態が保たれますが、
収納物の位置が明確でなかったり、
使用後に戻すルールが曖昧だと、再び乱雑になる恐れがあります。
「何かのきっかけで再発する改善」と評価します。
→ C(8点)
(5)習慣(しつけ)レベル
現在の状態では、工具の収納位置や戻し方に関する
表示・ルール・点検などが明確にされていないと推測されるため、
整頓状態の維持が属人化する可能性があります。
「徹底すべきルールを設定した改善」と評価します。
→ C(8点)
合計点数
12(成果) + 8(独自性) + 12(難易度) + 8(清潔) + 8(習慣) = 48点
5Sレベル:B(46~65点)
評価まとめ
今回の改善は「作業効率向上」という点で
とても有効な取り組みでしたが、
長期的に乱れを防ぐ仕組みの不在や、
収納の標準化不足が課題です。
「工具を戻す」「位置を守る」ことを
誰でも実行できる仕掛けを加えることで、
次の改善レベルへと進化できると期待しています。
今後の改善ポイント
✅ 工具ごとに定位置を明示(ラベルや型取り)
✅ 使用後に元に戻すルールを明文化
✅ 整頓状態をチェックする仕組みを導入する
ぜひ次回は、“誰が使っても乱れない”整頓状態を目指した
高レベルな改善報告をお待ちしています!