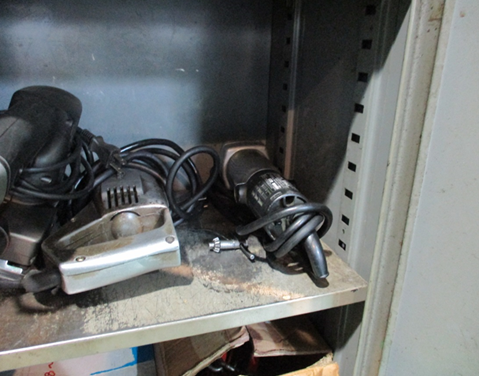
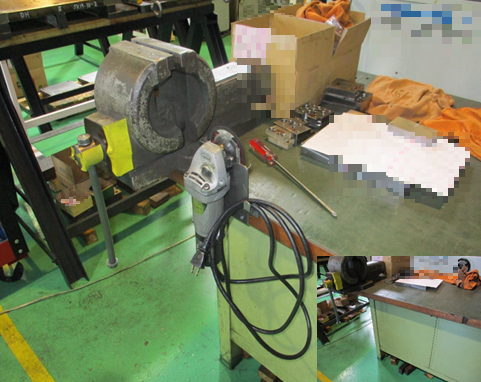
【結果/効果】
(なにが)
作業台にサンダーをセットしたので
(どうなった)
なおさなくてもよくなった。
1日平均で40秒短縮×20日
1カ月あたり:800秒削減
【専門家コメント】
サンダーが棚に収納されていて、使用のたびに
出し入れの手間が発生していた非効率な状態を、
作業台に専用の設置場所を設けることで、
作業中でもすぐに手に取れて、使用後もそのまま戻せるようにした改善ですね。
この改善によって、「収納・取り出す」というムダな動作がなくなり、
作業の流れが中断されることなく効率的に進められるようになります。
また、サンダーの定位置化によって整頓レベルも向上しており、
非常に実用性の高い改善です。
まずはこの問題に気づき、行動してくれたことに感謝します。
次に考えてほしいのは、
その設置場所が「誰が見ても専用とわかるかどうか?」という点です。
例えば、「サンダー専用」などの表示を付けたり、
定位置に色枠やシルエットを施すことで、
「誰でも戻せる」「乱れない」環境を実現できます。
5Sでは整頓のあとは「清潔」「しつけ」によって
維持される仕組みが重要になります。
ぜひこの視点で、さらなる改善にも取り組んでみてください。
次回の改善報告も楽しみにしています。
以下に、今回の「棚に収納していたサンダーを作業台に専用設置し、取り出し・片付けのムダを削減した改善」について、ご提示いただいた評価基準と記述表現に忠実に、厳しめの視点で評価を行います。
(1)成果の大きさ
サンダーを使用するたびに発生していた「出し入れ」の動作を削減し、
作業の流れを止めずに使用・片付けができるようになったことで、
作業効率の向上に確実に貢献しています。
ただし、対象が1工具に限られており、
生産性や安全面への影響は限定的と判断されるため、
「満足のいく成果である改善」と評価します。
→ B(12点)
(2)改善の独自性
作業台に専用の置き場所を設けるという発想は、
整頓の基本的な考え方に基づいたものであり、
類似の改善は多く見られます。
特別な工夫や発想の困難さは少ないため、
「よく似たタイプが多い改善」と評価します。
→ C(8点)
(3)改善の難易度
設置場所の確保や固定用具の準備など、
一定の作業は必要であったと考えられますが、
大がかりな加工や複雑な設置は不要であったと想定されます。
「標準的な時間でできた改善」と評価します。
→ B(12点)
(4)清潔レベル
サンダーの定位置が明確になったことで、
乱れにくい整頓状態が維持されやすくなっています。
ただし、設置場所に明示がない場合、
他の物が置かれるなどの再発の可能性があるため、
「同じ状況なら再発が起きにくい改善」と評価します。
→ B(12点)
(5)習慣(しつけ)レベル
置き場所が明確になっていることで、
使用後に戻す動作が習慣化しやすくなっていますが、
専用表示やルールが未整備であれば徹底が難しくなるため、
「徹底すべきルールを設定した改善」と評価します。
→ C(8点)
合計点数
12(成果) + 8(独自性) + 12(難易度) + 12(清潔) + 8(習慣) = 52点
5Sレベル:B(46~65点)
評価まとめ
今回の改善は、日常作業の中にある“探す・片付けるムダ”を見逃さず、
整頓レベルを高める効果的な取り組みでした。
今後は**「誰でも守れる仕組み化」や「表示による明確化」**を進めることで、
さらに評価の高い改善へとつながります。
今後の改善ポイント
✅ サンダー設置箇所に「専用表示」や輪郭線を追加する
✅ 他のよく使う工具にも同様の整頓を展開する
✅ 定位置の維持点検を日常作業に組み込む
こうした改善が積み重なることで、現場の効率と精度は確実に向上します。
次回の改善報告も楽しみにしています!