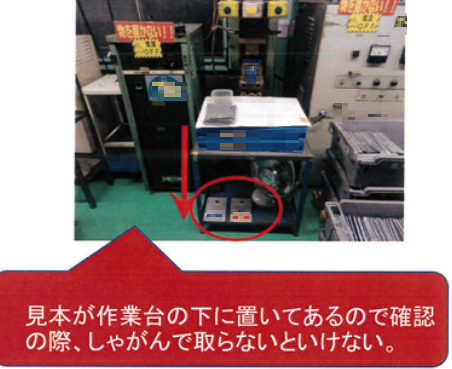
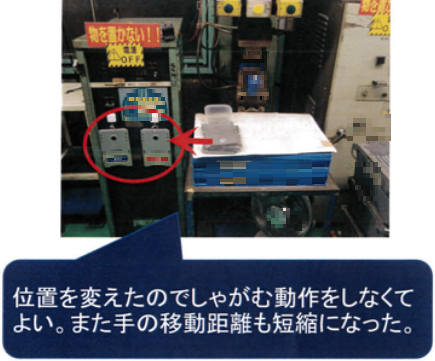
【結果/効果】
(なにが)
手の移動距離短縮
(どうなった)
50㎝が20㎝になった。
一日2回 60㎝距離が短縮
【専門家コメント】
見本が作業台の下に置かれており
確認の際にしゃがんで取り出す必要があったのを、
見本を作業台の横の見やすい位置に移動し、
立ったまま確認できるようにすることで、
手の移動距離が30cmほど短縮されると同時に、
しゃがむ動作を不要にすることにより
作業者の身体的負担も軽減した改善ですね!
小さな動作の改善ですが、積み重ねることで
作業効率の向上や疲労軽減につながります。
このような「作業しやすさ」に着目した視点は素晴らしいです!
ありがとうございました。
ただし、この改善にはまだ考えるべきポイントがあります。
例えば、
- 見本の位置は、本当に最適か?
→ 他の作業の邪魔にならないか、もっと取りやすい方法はないか? - 見本が増えた場合の管理方法は?
→ 収納スペースが足りなくなったとき、どう対応するのか? - 見本が乱れたり、紛失しないようにする仕組みは?
→ 定位置管理(ラベルやシルエット表示)や、定期点検のルールが必要では?
「置き場所を変えただけ」で終わらせず、
「どうすれば長期間維持できるか」 を考えてみてください!
次の改善報告では、さらに一歩踏み込んだ工夫を期待しています!
5Sレベルの評価
今回の改善を、5Sレベル評価でチェックしていきます。
(1)成果の大きさ
しゃがむ動作をなくし、手の移動距離を短縮したことで、
作業者の負担軽減や効率向上にはつながります。
しかし、影響範囲が限定的であり、生産性への劇的な変化は見込めません。
「成果がややもの足りない改善」と評価します。
→ C(8点)
(2)改善の独自性
作業しやすい位置に見本を移動するというのは、
整理・整頓の基本的な考え方に基づいた標準的な手法です。
特に斬新な工夫はなく、他の作業でもよく見られる改善のため、
「よく似たタイプが多い改善」と評価します。
→ C(8点)
(3)改善の難易度
見本の置き場所を変更するだけなので、
特別な技術も時間も必要ありません。
短時間でできるシンプルな改善のため、
「そんなに時間をかけない改善」と評価します。
→ C(8点)
(4)清潔レベル
見本の置き場所を変えただけでは、
時間が経つと元の場所に戻されたり、
別のものが置かれて乱れる可能性があります。
定位置を決める仕組みがなければ、
「何かのきっかけで再発する改善」と評価します。
→ C(8点)
(5)習慣(しつけ)レベル
見本を取りやすくする改善は良いですが、
「誰でも迷わず取り出せる仕組み」や
「元の状態を維持するルール作り」ができていないと、
そのうち改善の効果が薄れてしまいます。
長期的に維持する仕組みがないため、
「習慣化を促さない単発的な改善」と評価します。
→ D(4点)
合計点数:
8(成果) + 8(独自性) + 8(難易度) + 8(清潔) + 4(習慣) = 36点
5Sレベル:C(31~45点)
この改善は、「やればすぐできるが、長期的に維持されるか不透明な改善」 です。
作業のしやすさを向上させる良い視点はありますが、
「ただ場所を変えただけ」では、時間が経つと元に戻る可能性が高いです。
本当に意味のある改善にするためには、
✅ 見本の定位置を明確にし、誰でもすぐ分かるようにする(ラベルやシルエット表示)
✅ 見本が増えたときの管理ルールを決める(適切な収納スペースの確保)
✅ 定期的にチェックし、元の場所にあるか確認する仕組みを作る(点検表の導入)
こういった「維持と標準化」の仕組みがあれば、
BレベルやAレベルの改善へと引き上げることができます。
今回の改善を「一時的なもの」にせず、
「継続的に効果を発揮する仕組み」に発展させる工夫を期待しています!
次の改善報告を楽しみにしています。