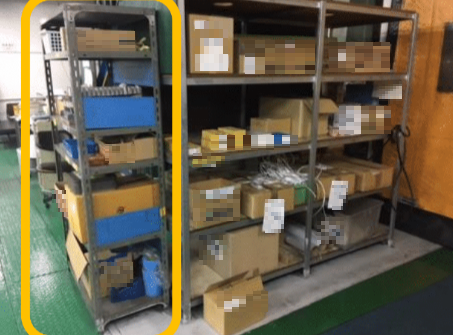
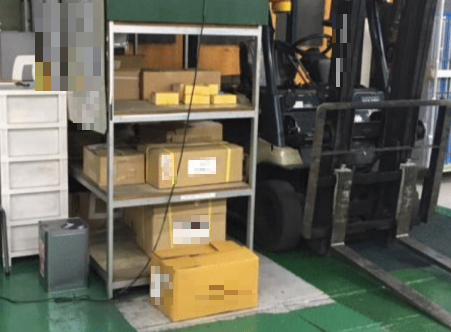
【結果/効果】
(なにが)
棚の整理を行い棚の撤去を行った。
(どうなった)
1㎡のスペースのムダがなくなった
【専門家コメント】
複数の棚が設置されていて、
スペースを非効率に使用していた状態だったのを、
部品の配置を見直し、不要な棚を撤去することで、
スペースを効率的に活用できるようにしたと同時に、
残った棚の中身も整然と配置して、
視認性を向上させた改善ですね!
限られた作業スペースを有効に使うことは、
作業効率の向上だけでなく、安全性向上にもつながります。
不要なものを取り除くことでスッキリし、
部品が探しやすくなるという点も素晴らしいです。
良い取り組みをありがとうございました!
しかし、この改善は今後も維持できるでしょうか?
例えば、
- 今後、部品の種類や量が増えたとき、スペースが再び圧迫されるリスクは?
→ 追加部品の収納ルールや、新たなレイアウト変更の基準は決まっているか? - 撤去した棚が必要になる可能性はないか?
→ 棚を減らしすぎて、収納不足にならないか? - 視認性をさらに向上させる工夫はあるか?
→ ラベル表示や色分けを活用し、よりわかりやすくできるか?
ただ「棚を減らした」だけでは、
時間が経つとまたスペースが圧迫される可能性があります。
「長期的に維持できる仕組み」 を考え、
さらなるレベルアップを目指してみてください!
次回の改善報告では、「維持・標準化の工夫」 にも踏み込んだ取り組みを期待しています!
5Sレベルの評価
今回の改善を、5Sレベル評価でチェックしていきます。
(1)成果の大きさ
不要な棚を撤去し、スペースを有効活用できるようになったことで、
作業エリアが広くなり、視認性も向上しました。
ただし、作業時間の短縮や生産性向上にどの程度寄与したかが不明なため、
「やや大きい成果」と評価します。
→ A(16点)
(2)改善の独自性
「不要な棚を撤去し、配置を見直す」という手法は、
整理・整頓の基本的な考え方であり、特に目新しさはありません。
よく見られる改善のため、「よく似たタイプが多い改善」と評価します。
→ C(8点)
(3)改善の難易度
棚の撤去や部品の再配置には、ある程度の時間と労力が必要ですが、
特別な技術を要するものではなく、標準的な作業の範囲内です。
「標準的な時間でできた改善」と評価します。
→ B(12点)
(4)清潔レベル
スペースを広くしたことで一時的には改善されていますが、
今後、部品の種類や量が増えた際に、
再び棚が必要になったり、乱雑になる可能性があります。
「何かのきっかけで再発する改善」と評価します。
→ C(8点)
(5)習慣(しつけ)レベル
整理後の状態を維持するためのルールがなければ、
時間が経つとまたスペースが埋まり、元に戻る可能性があります。
「徹底すべきルールを設定した改善」と評価します。
→ C(8点)
合計点数:
16(成果) + 8(独自性) + 12(難易度) + 8(清潔) + 8(習慣) = 52点
5Sレベル:B(46~65点)
今回の改善は、「スペースを有効活用する良い取り組みだが、維持管理に課題がある改善」 です。
一時的にスペースは広くなりましたが、
「長期的に維持する仕組みがなければ、再び物が増えてしまうリスクがある」 ため、
さらなる対策が必要です。
今後の課題として考えるべきポイント
✅ 部品の増加に対応できるよう、収納ルールを明確にする
✅ ラベルや色分けを活用し、視認性をさらに向上させる
✅ 定期的な点検を実施し、不要な棚やスペースが再び増えないよう管理する
せっかくの改善を「一時的なもの」で終わらせず、
「持続可能な管理の仕組み」 を取り入れて、
より高いレベルの改善を目指しましょう!
次の改善報告では、「維持管理の工夫」 にも踏み込んだ取り組みを期待しています!