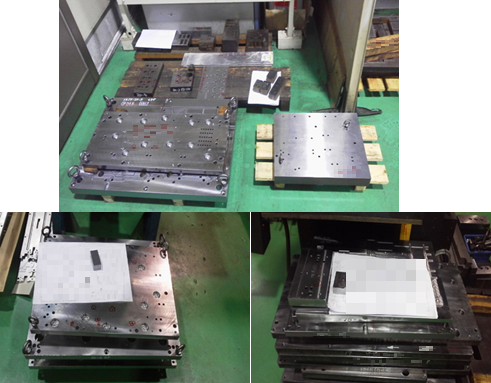
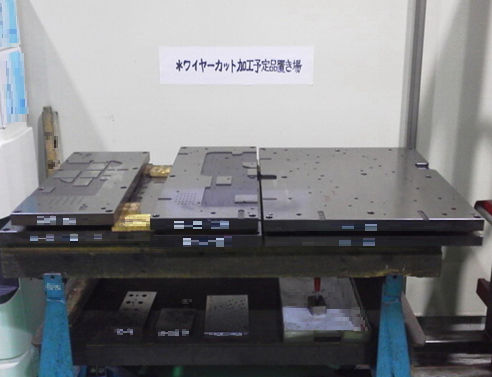
【結果/効果】
(なにが)
次に加工する材料が。
(どうなった)
一目で判り、探す時間が無くなった。
【専門家コメント】
これはワイヤーカット加工を施行する
予定のある部品がバラバラに置いてあったのを
その置き場所をつくって一か所に集める改善です
このことによって迷わなくてひと目でわかり
作業にスッと取り掛かれることで
前段取りの時間を短縮できると共に
作業そのものへの集中力も増しそうです
素晴らしい改善をありがとうございます
ただ心配になるのは、この大きなスペースの確保は
よほど余裕がある工場でないと難しく
タイミングによっては確保できない場合が多いですよね
加工対象の製品は金型なので
すべてにワイヤーカットが必要なわけでもなく
加工の必要がない日はデッドスペースとなります
それはそれで別の意味に効率が悪くなります
もし場所に余裕がない場合は
置き場所を柔軟に確保するルールが必要になり
最適なルールづくりが次の課題になるでしょうか
ぜひ全員で良いアイデアを考えて
試行錯誤で最適案を見つけてください