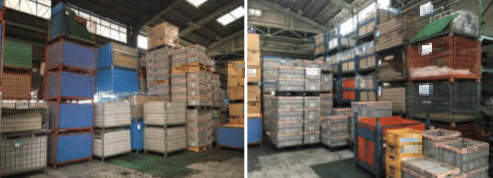
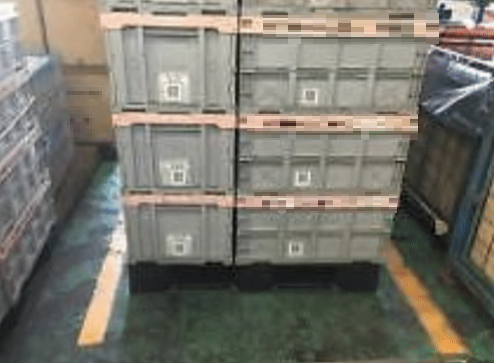
【結果/効果】
(なにが)
パンチングの不要なパレットを
(どうなった)
整理した
【専門家コメント】
パンチング加工が不要なプラスチックパレットが
他の種類のパレットと混在してバラバラに置かれていたため
格納スペースの効率がとても悪かったが
それを種類別に整理・整頓すると同時にラインを引くことで
スッキリ収納できるようになった改善ですね。
この改善で、作業スペースの有効利用が
進みましたね。素晴らしい取り組み、
ありがとうございます!
さらなる改善として、
「なぜ混在してしまったのか?」という
原因を掘り下げてみましょう。
考えられる理由としては、
- パレットの種類ごとの明確な識別方法がない
- 新しいパレットが入った際の
格納ルールが不明確 - 担当者間での情報共有が不足している
これらの点を改善するためには、
- パレットの種類ごとに色分けやラベリングをする
- 新しいパレットを格納する際の
ルールを明確にし、全員で共有する - 定期的な情報共有の場を設ける
などが有効です。
次なるステップでこれらの改善を
実施していただければ、より効率的で
快適な作業環境が実現します。
引き続き素晴らしい改善の報告を
楽しみにしています!