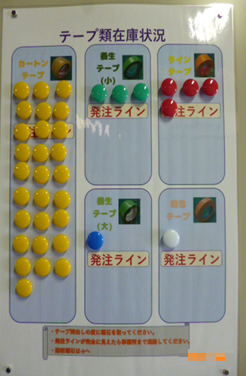
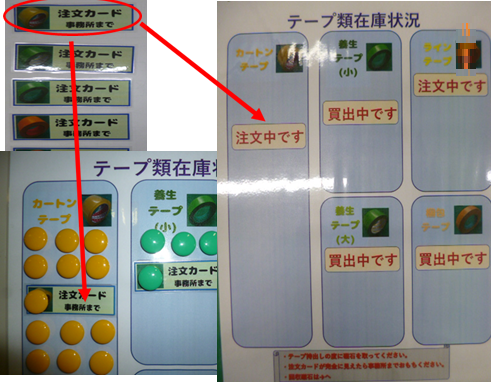
【結果/効果】
(なにが)
テープの発注状況がわかりやすくなった
(どうなった)
注文状況が一目でわかるようになったので
確認作業がなくなった。
一日平均10秒短縮X20日
1ヶ月200秒短縮
200円の削減
【専門家コメント】
テープの在庫状況はボードで可視化されていたものの、
「注文中」か「発注済」かの状態が不明確で、
その都度確認作業が必要だった状態を、
ボード内に明示的なエリアを追加して、
発注状況をすぐに把握できるようにした改善ですね。
この改善により、在庫状況だけでなく発注プロセスの可視化が実現され、
関係者間の情報共有がスムーズになり、
確認作業のムダや、発注モレ・重複のリスクも軽減される
非常に実務効果の高い整頓改善です。
まずはこの業務フロー上の“見えにくいムダ”に気づいてくれたことに感謝します。
今後さらに効果を高めるためには、
「誰が」「いつ」発注したかの記録欄を設けたり、
発注のルールやタイミングを標準化することで、
習慣(しつけ)レベルの改善に進化できます。
5Sでは、情報の整頓と伝達の明確化も重要なテーマです。
ぜひこの改善をきっかけに、仕組みとしての定着まで取り組んでみてください。
次回の改善報告も楽しみにしています。
以下に、今回の「在庫管理ボードに注文中・発注済のエリアを追加し、テープの発注状況を明確化した改善」について、ご提示いただいた評価基準と記述表現に忠実に、厳しめの視点で評価いたします。
(1)成果の大きさ
在庫状況は見える化されていたものの、
「発注済かどうか」が分かりづらく、確認作業に手間がかかっていた状態を、
エリアを明示することで一目で状況が把握できるように改善した点は、
業務の効率化と発注ミス防止に効果的です。
ただし、対象が特定の資材(テープ)に限定されており、
工場全体への影響としては限定的なため、
「満足のいく成果である改善」と評価します。
→ B(12点)
(2)改善の独自性
発注状況を分類表示する方法は、
情報整頓の基本であり、事務・現場を問わず
よく見られる手法のひとつです。
特別な発想や工夫は求められないため、
「誰でも思いつく改善」と評価します。
→ D(4点)
(3)改善の難易度
ボードに「注文中」「発注済」といったエリアを追加する作業は、
表示の作成と貼り付け程度で完了でき、
数分~15分程度で実施可能な簡単な内容です。
→ D(4点)
(4)清潔レベル
状態の分類によって在庫情報が整理され、
発注忘れや重複といった業務トラブルの未然防止に
つながっている点は評価できます。
ただし、分類の更新が手動であるため、
操作ミスや記入漏れで再発する可能性もあるため、
「同じ状況なら再発が起きにくい改善」と評価します。
→ B(12点)
(5)習慣(しつけ)レベル
発注状況の表示という改善により、
一定の管理ルールに沿った運用が促されますが、
「誰が」「いつ」更新するかが明文化されていない場合、
運用が属人的になりやすいため、
「徹底すべきルールを設定した改善」と評価します。
→ C(8点)
合計点数
12(成果) + 4(独自性) + 4(難易度) + 12(清潔) + 8(習慣) = 40点
5Sレベル:C(31~45点)
評価まとめ
今回の改善は、情報の見える化によって判断や確認作業を減らした、
実務に根差した良い整頓改善でした。
ただし、独自性と難易度の低さ、更新ルールの不在が評価を抑える要因です。
今後の改善ポイント
✅ 「誰が・いつ発注したか」記録欄を追加する
✅ 発注状況の更新ルールを明文化・掲示する
✅ 他の資材や備品の管理にも同様の仕組みを展開する
情報整理も5S活動の重要な一環です。
次回は、仕組み化・ルール化まで踏み込んだ報告を期待しています。