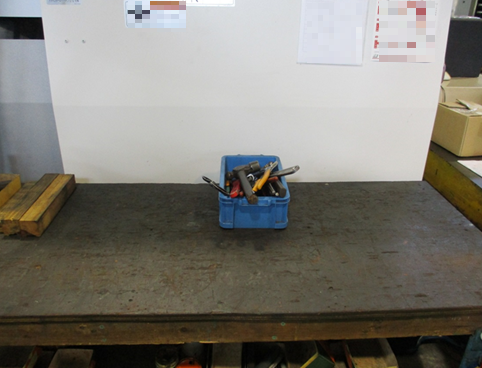
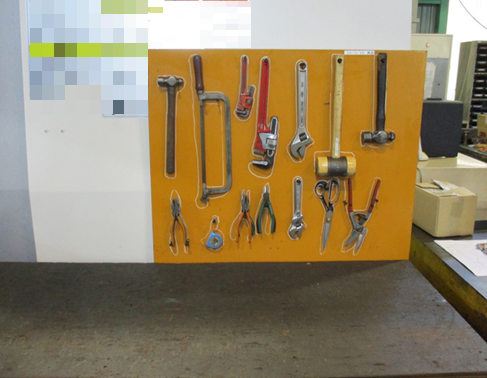
【結果/効果】
(なにが)
工具を探すムダや取り出すムダが。
(どうなった)
1日平均で48秒短縮×20日
1カ月あたり:960秒削減(960円削減)
【専門家コメント】
これまで乱雑に箱の中にしまっていた工具を
板を作成して形跡整頓を実現した事例ですね。
形跡整頓したことによって
収まる場所に収まるものが収まるという
整頓の基本ができました。
これがまさに、モノの置き方の標準化です。
とても素晴らしい改善をありがとうございます。
さて、次に考えていただきたいことは、
誰でも取り出せて、誰でもが返却できる仕組みを
構築していただければと思います。
このカタチをみて、型通りに道具を置くことができるのは
この工具がここにあることを知っているヒトだけです。
もしかすると道具の全貌を知らない今日入社した新人なら
あるいは少し変わった考え方をする同僚なら
逆に置いたり、どこかに置いてきてしまったりする
かもしれません。
そこで次の改善はやはり、ここが何の置き場なのか?
そこに何を置くのか、それを明確にするために
しっかり表示することですね。
表示こそ整頓の要となります。
次回も素晴らしい改善報告を心待ちにしています。