
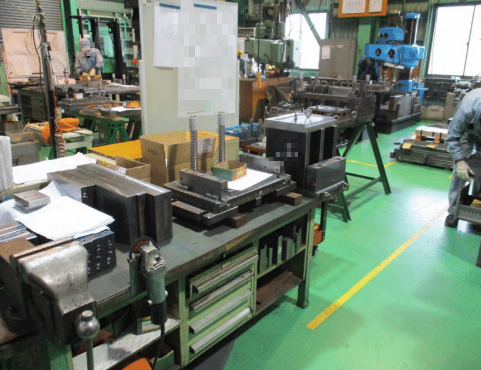
【結果/効果】
(なにが)
歩くムダが
(どうなった)
1日平均で30秒短縮X20日
(1カ月20日稼働で試算してください)
1カ月あたり:600秒削減
600円/月削減
【専門家コメント】
サンダーを取るために、毎朝ロッカーまで
取りに行っていたムダを
サンダーを使用する場所に置くことで効率化した
改善ですね。
使用する頻度の高いものは手元に置いておくという
5Sの進化系を見せていただき、ありがとうございました。
サンダーを取りに行くことが当たり前になっていると
なかなかこの歩行のムダに気づかないのですが
そこに気づかれたのはとても素晴らしいと感じました。
改善活動ご苦労さまでした。
今後についての提案ですが、
このサンダーについてさらにランクアップさせる
改善をお願いできればと思います。
写真を見る限りで恐縮ですが、
サンダーの置き場所は明確になっていそうですが、
明示が無いようです。
ここは3定の原則で、定位・定品・定量をこころがけて
みてください。
具体的には、
・定位として、置き場所の明示
・定品として、サンダーの個別識別表示
・定量として、ここに置くのは決められたサンダーのみの明示(定位と定品で実現)
を実施してみてくださいね。
その後は、ぜひ横展開してみてくださいね
では、次なる改善を楽しみにしております。