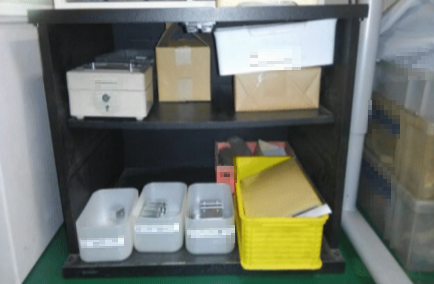
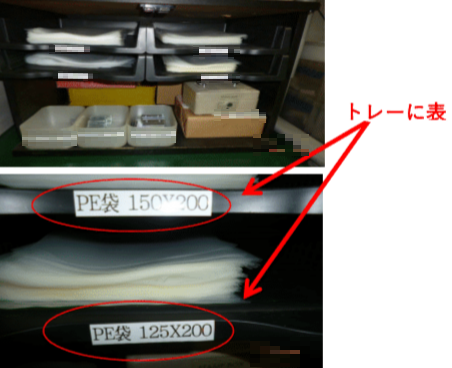
【結果/効果】
(なにが)
セットする度に探すムダとPE袋の場所までの
移動していた。
(どうなった)
セットする場所にPE袋を設置し、表示をした。
一回のセットで30秒の短縮ができた。
【専門家コメント】
以前はPE袋を探したり、保管場所まで移動する必要がありましたが、
作業セット場所に直接PE袋を設置し、さらに各サイズのPE袋の置き場に
明確な表示を行って識別を容易にした改善ですね!
これにより、PE袋を探す時間と移動時間が削減され、1回のセットあたり
30秒の時間短縮を実現したとのこと。
作業の効率化に大きく貢献する素晴らしい取り組みですね。
日常の業務で気づいた問題点にしっかり対応していただき、
ありがとうございます。
次に考えていただきたいのは、この改善を長期的に維持し、
さらに向上させるための仕組み作りです。以下の点を意識してみてください:
- 定期的なPE袋の在庫確認と補充ルール
時間短縮が実現されても、PE袋が不足してしまうと元に戻ってしまうため、
定期的に在庫を確認するルールを設定しましょう。
例えば、一定の量を下回ったらすぐに補充する仕組みを作り、
誰がどのタイミングで確認・補充するかを明確にすると良いです。 - 表示ラベルのメンテナンス
各サイズのPE袋の置き場に表示をしているとのことですが、
ラベルが汚れたり、剥がれたりしないよう、定期的に確認し、
必要に応じて交換できるようにしておくことが重要です。
表示がしっかりしていると、初めての人や他のメンバーでも
すぐに識別できる環境が維持されます。 - 作業場所のさらなる効率化
今回の改善で作業効率が向上しましたが、他の作業エリアや
関連するアイテムでも同じような工夫ができるかもしれません。
例えば、PE袋以外の消耗品の配置や管理を見直すことで、
さらなる効率化が図れる可能性があります。定期的に作業セットの
状況を見直し、新たな改善点を見つけることが大切です。 - フィードバックの活用
実際に現場でこの改善を使っているメンバーから定期的に
フィードバックを集めてみてください。現場の声を聞くことで、
さらに効率的な方法や新しい課題が見つかることがあります。
チーム全体で共有しながら、改善を進めるとより良い結果が
期待できます。
今回の改善は、作業効率を大幅に向上させる素晴らしい取り組みです。
しかし、今後も維持し、さらに発展させるためには、継続的な改善の
意識が重要です。ぜひこの成果を基に、さらなる効率化や職場改善に
取り組んでいってください。次の報告書を楽しみにしています!